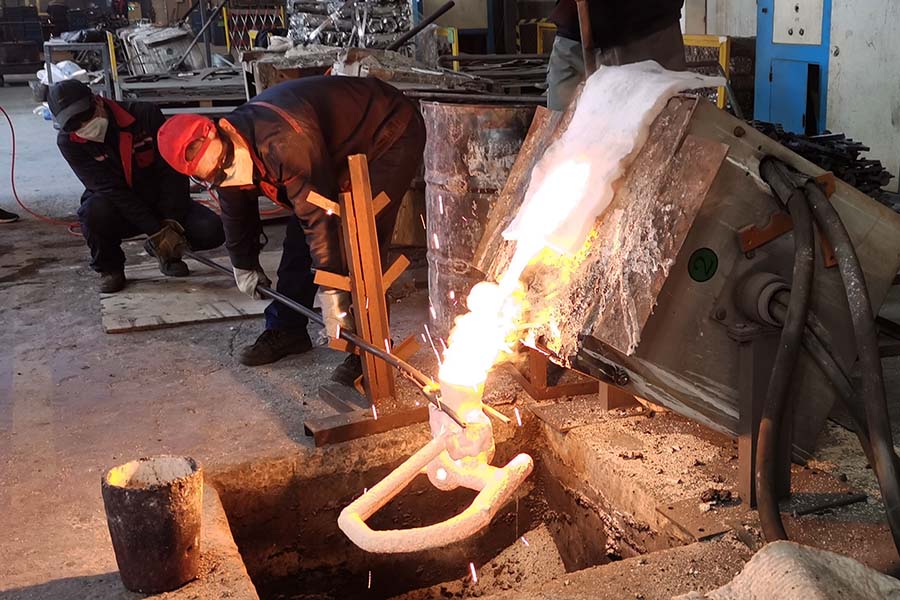
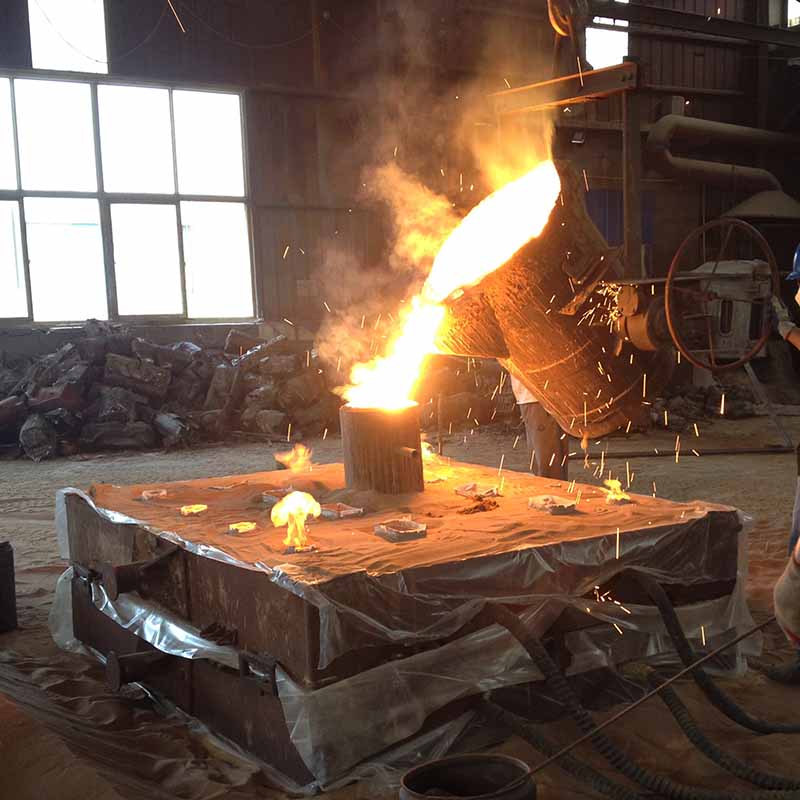
Gieten is ien fan 'e ierste metoaden foar it foarmjen fan metalen bekend by minsken. It betsjut yn 't algemien dat it smelte metaal yn in fjoerwurkfoarm giet mei in holte fan' e foarm dy't makke wurde moat, en lit it fêstigje. Wannearsolidified, de winske metalen foarwerp wurdt nommen út 'e fjoerstien mal itsij troch brekken de mal of troch nimme de mal útinoar. It fersterke objekt wurdt casting neamd. Dit proses wurdt ek wol oprjochting neamd, en it moderne fabryk dat him rjochtet op it jitten fan metalen dielen wurdt neamdgieterij.
1. Skiednis fan Casting Process
It casting proses waard wierskynlik ûntdutsen om c 3500 f.Kr. yn Mesopotaamje. Yn in protte dielen fan 'e wrâld waarden yn dy perioade koperen billen en oare platte foarwerpen draaid yn iepen mallen makke fan stien of baktklaai. Dizze mallen wiene yn essinsje yn ien stik. Mar yn lettere perioaden, doe't rûne objekten moasten makke wurde, waarden sokke mallen yn twa of mear dielen splitst om it weromlûken fan 'e rûne objekten te fasilitearjenDe Brûnstiid (c 2000 f.Kr.) brocht folle mear ferfining yn it castingproses. Foar it earst miskien in kearn foar it meitsjen fan holle bûsen yn 'e objekten útfûn. Dizze kearnen waarden makke fan bakte klaai.Ek it proses fan cire perdue of ferlern waaks waard wiidweidich brûkt foar it meitsjen fan sieraden en moai wurk.
De casting technology is troch de Sinezen gâns ferbettere fan om 1500 f.Kr. Dêrfoar is d'r gjin bewiis foar castingaktiviteit fûn yn Sina. Se lykje net geweldich west te hawwenbekend mei de cire perdue proses noch brûkte it wiidweidich, mar ynstee spesjalisearre yn multi-stik mallen foar it meitsjen fan heul yngewikkelde banen. Se bestege in protte tiid yn it perfeksjonearjen fan de mal ta it lêste detail sa dat ampereltse ôfwurking wie nedich op it casting makke fan de mallen. Se makken wierskynlik stikmallen mei soarchfâldich ynrjochte stikken, nûmere tritich of mear. Eins binne in protte fan sokke skimmels ûntdutsenuring argeologyske opgravings yn ferskate dielen fan Sina.
Indus Valley Civilization is ek bekend om syn wiidweidige gebrûk fan casting fan koper en brûns foar ornaments, wapens, ark en gebrûksfoarwerpen. Mar d'r wie net folle fan ferbettering yn 'e technology. Fan de farious foarwerpen en figueren dy't ôfgroeven waarden út de Indus Valley sites, se lykje te wêzen bekend mei alle bekende casting metoaden lykas iepen skimmel, stik skimmel en it cire perdue proses.
Hoewol Yndia koe wurde byskreaun mei de útfining fan kroes stiel, net folle fan izeren oprjochting wie evident yn Yndia. D'r is bewiis dat izeren stifting om 1000 f.Kr. begon wie yn Syrië en Perzje. It docht blikendatizer-castingtechnology yn Yndia is yn gebrûk west fan 'e tiden fan' e ynvaazje fan Alexander de Grutte, om 300 f.Kr.
De ferneamde izeren pylder dy't no tichtby de Qutb-minar yn Delhi leit, is in foarbyld fan 'e metallurgyske feardichheden fan âlde Yndianen. It is 7,2 m lang en is makke fan suver smeedber izer. Dit wurdt oannommen te wêzen fan deperioade fan Chandragupta II (375-413 AD) fan 'e Gupta-dynasty. De roestsnelheid fan dizze pylder, dy't bûten yn 'e iepen loft stiet, is praktysk nul en sels it begroeven diel roest mei in ekstreem stadich taryf. Ditmoat earst getten west hawwe en dan nei de definitive foarm hammere.
2. Foardielen en beheinings
It castingproses wurdt wiidweidich brûkt yn 'e fabrikaazje fanwegen syn protte foardielen. Gesmolten materiaal streamt yn elke lytse seksje yn 'e skimmelholte en as sadanich elke yngewikkelde foarm - ynterneof ekstern - kin makke wurde mei it castingproses. It is mooglik om praktysk elk materiaal te jitten, itsij ferro as non-ferro. Fierder, de nedige ark nedich foar casting mallen binne hiel ienfâldich engoedkeap. As gefolch, foar proefproduksje as produksje fan in lyts lot, is it in ideale metoade. It is mooglik yn casting proses, te pleatsen it bedrach fan materiaal dêr't it is krekt nedich. Dêrtrochgewichtsreduksje yn ûntwerp kin wurde berikt.Castingswurde oer it generaal unifoarm fan alle kanten ôfkuolle en dêrom wurde se ferwachte dat se gjin rjochtingseigenskippen hawwe. Der binne bepaalde metalen en alloydat kin allinnich wurde ferwurke troch casting en net troch in oar proses lykas smeden fanwege de metallurgyske oerwagings. Castings fan elke grutte en gewicht, sels oant 200 ton kinne wurde makke.
Lykwols, de dimensionale krektens en oerflak finish berikt troch normaalsân-casting prosessoe yn in protte gefallen net adekwaat wêze foar definitive tapassing. Om dizze gefallen yn oerweging te nimmen, wat spesjale castingprosessen lykas diecasting binne ûntwikkele, de details dêrfan wurde jûn yn lettere haadstikken. Ek is it sângietproses foar in part arbeidsintensyf en dêrom binne der in protte ferbetteringen op rjochte,lykas masine moulding en gieterij meganisaasje. Mei guon materialen is it faak lestich om defekten te ferwiderjen dy't ûntsteane út it focht oanwêzich ynsân castings.
3. Casting Terms
Yn de folgjende haadstikken soe de details fan sân-casting, dy't it basisproses fan casting fertsjintwurdiget, sjoen wurde. Foardat jo yn 'e details fan it proses gean, soe it definiearjen fan in oantal casting wurdskatwurden wêzegaadlik.
Flask- In foarmkolf is ien dy't de sânskimmel yntakt hâldt. Ofhinklik fan 'e posysje fan' e fles yn 'e skimmelstruktuer, wurdt it ferwiisd troch ferskate nammen lykas drag, cope en wang. It is makke fan houtfoar tydlike applikaasjes of mear algemien fan metaal foar lange-termyn gebrûk.
Sleep- Legere moulding kolf
Cope- Boppeste moulding kolf
Wang- Intermediate moulding kolf brûkt yn trije-dielige moulding.
Patroan- Pattern is in replika fan it definitive objekt dat moat wurde makke mei wat oanpassings. De skimmelholte wurdt makke mei help fan it patroan.
Skilje line- Dit is de skiedsline tusken de twa foarmflessen dy't de sânskimmel útmakket. Yn split patroan is it ek de skiedsline tusken de twa helten fan it patroan
Bottom Board- Dit is in boerd normaal makke fan hout, dat wurdt brûkt by it begjin fan it meitsjen fan mallen. It patroan wurdt earst op it ûnderste planke hâlden, der wurdt sân op struid en dan wurdt it ramt yn it slepen.
Facing Sand- De lytse hoemannichte koalstofhoudend materiaal besprinkeld op it binnenste oerflak fan 'e foarmholte om bettere oerflakfinish te jaan oan' e castings
Molding Sand- It is it nij tariede fjoerwurk materiaal dat wurdt brûkt foar it meitsjen fan de skimmelholte. It is in mingsel fan silica klaai en focht yn passende ferhâldingen te krijen de winske resultaten en it omgiet depatroan wylst it meitsjen fan de mal.
Backing Sand- It is wat it measte útmakket fan it fjoervast materiaal fûn yn 'e skimmel. Dit bestiet út brûkt en ferbaarnd sân.
Kearn- It wurdt brûkt foar it meitsjen fan holle holtes yn castings.
Giet Basin- In lytse trechterfoarmige holte oan 'e boppekant fan' e mal dêr't it gesmolten metaal yn getten wurdt.
Spure- De trochgong dêr't it smolten metaal út it giebekken troch de skimmelholte komt. Yn in protte gefallen kontrolearret it de stream fan metaal yn 'e mal.
Runner- De trochgongen yn 'e ôfskiedingsflak dêr't smolten metaalstream troch regele wurdt foardat se de skimmelholte berikke.
Poarte- It eigentlike yngongspunt dêr't gesmolten metaal de malholte yn komt.
Chaplet- Chaplets wurde brûkt om kearnen yn 'e foarmholte te stypjen om te soargjen foar har eigen gewicht en de metallostatyske krêften te oerwinnen.
Chill- Chills binne metalen foarwerpen, dy't wurde pleatst yn 'e mal te fergrutsjen de koeling taryf fan castings te foarsjen unifoarm of winske cooling rate.
Riser- It is in reservoir fan gesmolten metaal foarsjoen yn 'e casting, sadat hyt metaal werom kin streame yn' e skimmelholte as d'r in fermindering is yn it folume fan metaal fanwege solidifikaasje
4. Sand Mold Making Proseduere
De proseduere foar it meitsjen fan in typyske sânfoarm wurdt beskreaun yn 'e folgjende stappen:
Earst wurdt in ûnderste boerd pleatst op it foarmplatfoarm of op 'e flier, wêrtroch it oerflak sels is. De slepe moulding flask wurdt holden op 'e kop op' e boaiem board tegearre mei de sleep diel fan 'epatroan yn it sintrum fan 'e fles op it boerd. D'r moat genôch klaring wêze tusken it patroan en de muorren fan 'e flesse dy't fan' e oarder wêze moatte fan 50 oant 100 mm. Dry facing sân wurdt sprinzge oerit boerd en patroan om in nonsticky laach te jaan. Fris taret foarmsân fan de nedige kwaliteit wurdt no yn 'e slepen en op it patroan getten oant in dikte fan 30 oant 50 mm. De rest fan 'e dragfles isfolslein fol mei de reservekopy sân en unifoarm rammed te kompakt it sân. It stommen fan it sân moat goed dien wurde om it net te hurd te kompaktjen, wat it ûntkommen fan gassen dreech makket,ek net te los, sadat de skimmel net genôch krêft hawwe soe. Nei't it ramjen foarby is, wurdt it oerstallige sân yn 'e flesse folslein skuorre mei in flakke balke nei it nivo fan' e flessekanten.
No, mei in luchtdraad, dat is in draad fan 1 oant 2 mm diameter mei in spitse ein, wurde luchtgatten makke yn 'e slepen nei de folsleine djipte fan' e flesse en ek nei it patroan om it fuortheljen fan gassen te fasilitearjen tidens castingfersteuring. Dit foltôget de tarieding fan it slepen.
De ôfmakke sleepfles wurdt no rôle oer nei it ûnderste boerd dat it patroan bleatstelle lykas werjûn yn 'e foto. Mei in slick wurde de rânen fan sân om it patroan repareare en de kophelte fan it patroan wurdt pleatst oerde slepe patroan, aligning it mei help fan dowel pins. De cope fles boppe op 'e slepen leit aligning wer mei help fan de pinnen. It droege ôfskiedssân wurdt oer de sleep en op it patroan strutsen.
In sprue pin foar it meitsjen fan de sprue passaazje leit op in lytse ôfstân fan likernôch 50 mm fan it patroan. Ek, riser pin as nedich wurdt bewarre op in passend plak en farsk taret molding sân fergelykber mei datfan de slepe tegearre mei it backing sân wurdt besprinkeld. It sân wurdt yngeand ramd, oerskot sân skrast en lucht gatten wurde makke oeral yn 'e cope as yn' e slepen.
De spuitpin en de e riserpin wurde foarsichtich út 'e flesse helle. Letter wurdt it jitbekken ticht by de boppekant fan 'e sprue ôfsnien. De cope wurdt skieden fan it slepen en alle losse sân op 'e cope en slepe ynterfacefan it slepen wurdt ôfblaasd mei help fan balgen. No wurde de cope en de slepepatroanhelten weromlutsen troch de tekenspikes te brûken en it patroan rûnom te slaan om de skimmelholte wat te fergrutsjen, sadat demold muorren wurde net bedoarn troch it weromlûken patroan. De rinners en de poarten wurde foarsichtich yn 'e mal snien sûnder de skimmel te bedjerren. Eltse oerstallige of losse sân fûn yn 'e rinners en skimmelholte wurdt blaasdfuort mei de balgen. No, it facing sân yn 'e foarm fan in paste wurdt tapast oer de skimmel holte en de rinners, dat soe jaan de ôfmakke casting in goede oerflak finish.
In droege sânkearn wurdt taret mei in kearnkast. Nei it passend bakken wurdt it yn 'e foarmholte pleatst lykas werjûn yn' e foto. De cope wurdt ferfongen op it slepen it fersoargjen fan de ôfstimming fan de twa troch middel fan depins. In gaadlik gewicht wurdt hâlden op 'e cope om te soargjen foar de opwaartse metallostatyske krêft by it gieten fan gesmolten metaal. De skimmel is no, lykas werjûn yn 'e foto, klear om te jitten.
Posttiid: Dec-25-2020